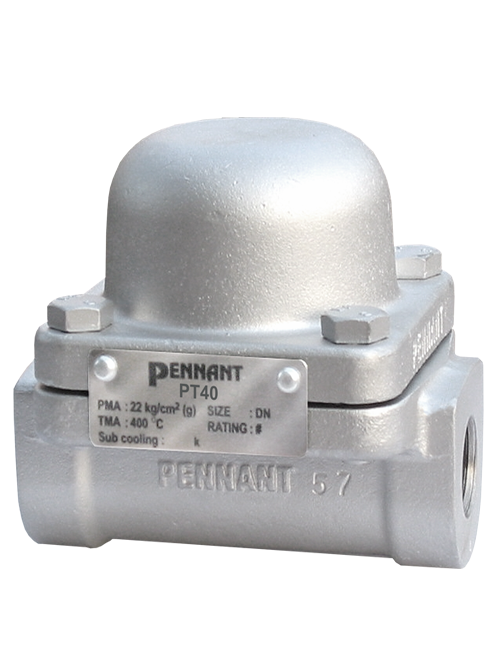
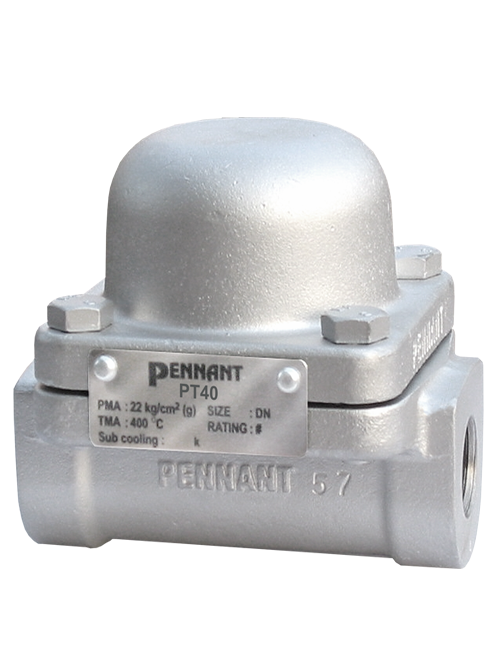
Pennant offers a wide variety of Steam Traps & Pipeline Accessories for the effective removal of condensate from steam systems without the loss of steam, catering to various industrial requirements such as;
Offered by Pennant USA
We provide steam trap surveys & audits which look at your entire set up to provide you with a customized solution to enhance energy saving, environmental performance, safety and regulatory compliance.
Pennant offers a range of flow control products with a variety of valves in forged/cast steel construction, for different industrial applications like;
Pennant Rotary Steam Control Valves for Food & Beverage Application Solutions – By Kevin Rasmussen.